薄肉ワークの高精度加工を実現
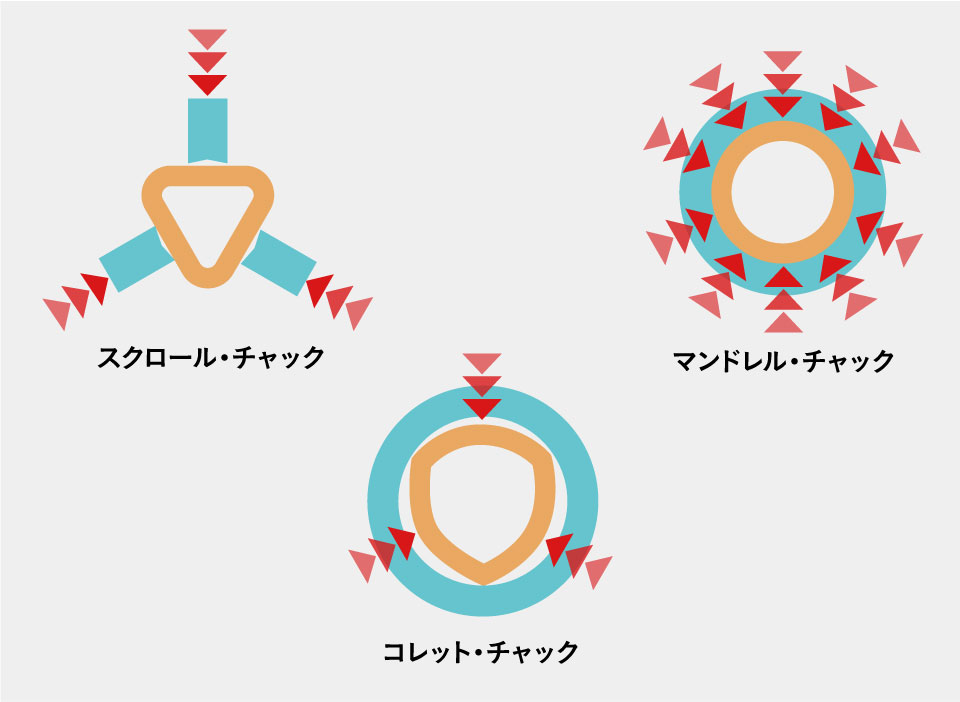
内面研削を必要とするワーク(工作物)は真円度や表面粗さだけでなく外径に対する振れ(同軸度)も併せて要求されることが多く、特に薄肉のワークについては把持による変形が課題となります。
ワークの把持にはいくつか方式がありますが例えば図のように、一般的に用いられているスクロール・チャックは3か所の爪でワークを把持するため三角形状の変形が発生するケースが多く、コレット・チャックではリング形状を分割してワークを把持するためいびつな変形が見られます。
また、マンドレル・チャックは円周全面で均一にワークを把持するため歪みが少ないというが特徴ですが、把持可能なワークが1種類に限定され、汎用性や高能率という点で難点があります。
こうした把持による形状精度の悪化を回避するため、これまでボールベアリング部品などの内面研削加工に用いてきた方式を応用した汎用性の高い2ロール1シュー主軸を新たに開発しました。
STG-6Nロール主軸仕様の特徴と事例
新たに開発した2ロール1シュー主軸を当社が 製造、販売しているCNC内面研削盤STG-6Nに搭載することにより、薄肉ワークの高精度加工を実現しました。
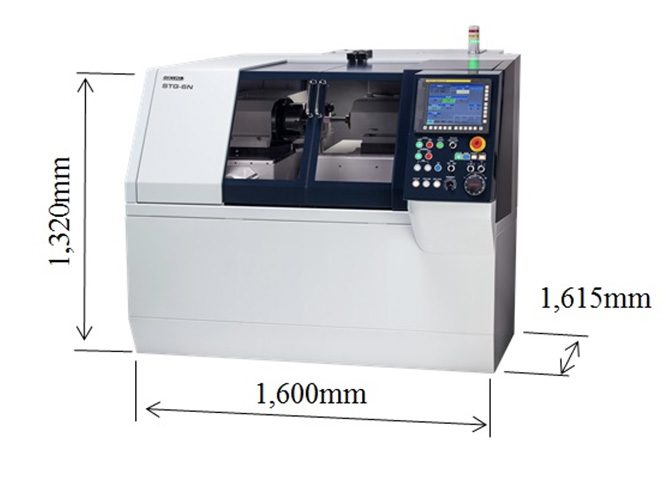
加工サイズ | 穴径×長さ | 最大φ100×100mm | |
---|---|---|---|
スピンドル | SSPG042-T100 | Max.42,000min-1 | |
主軸 | 回転数 | Max.1,200min-1 | |
チャック | 6インチスクロールチャック | ||
X/Zテーブル | ストローク | 200mm/300mm | |
ドレッサ | 単石ダイヤ仕様 |
2ロール1シュー主軸とは同期回転する2つのロールでワーク外径を挟んで回転させ、固定されたシューに外径を倣わせて内径を加工する構造です。
2つのロールはタイミングベルトを介し、モータにより同期駆動され、ワーク端面は固定されたバッキングプレートとバネ力で押さえるフロントプレートにより支持される。2つのロールの開閉によりワークの着脱を行う機構になっており、この開閉距離を長くすることで1種類のツーリング部品で様々なワークサイズに対応できます。
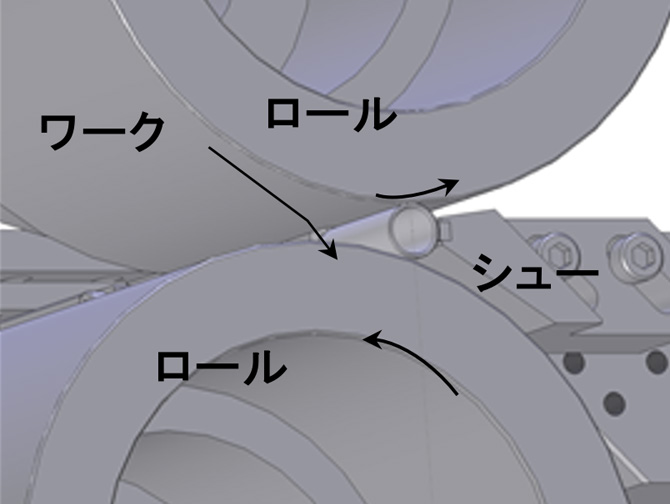
本主軸の場合、ワークを外径側のシューと内径側の砥石で挟み込む形で加工することになるため、基準となるワークの外径に対して肉厚が均一となり、加工後の外径に対する内径の同軸度が飛躍的に良くなり、またチャック主軸に比べ把持によるワークの変形が小さく真円度の向上が期待できるため、把持による変形が無視できない薄肉のワーク(例えば直径φ30で肉厚1mmなど)に適しています。下図左が加工基準となる外径の真円度であり、下図右が加工した内径の真円度を表します。
基準外径真円度が0.39μmに対し加工内径真円度は0.35μmであり、外径形状をほぼ転写したような形状となっており、前加工の外径真円度をセンタレス研削等によりしっかり確保できていれば内径真円度と同軸度はおのずと良くなることが分かります。
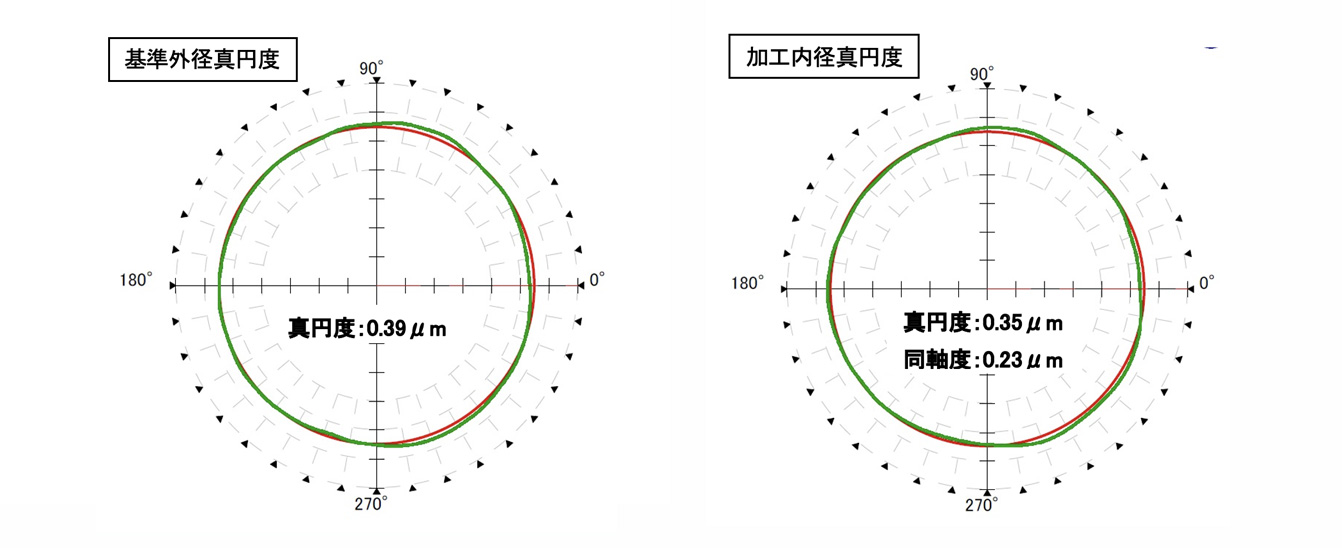
把持による変形の影響を受けやすい薄肉のワークの高精度加工という課題解決のひとつとしてSTG-6Nロール主軸仕様による加工事例を紹介しました。これはボールベリングや自動車部品を代表とする精密部品の量産現場で培ってきた技術を汎用内面研削盤に応用した例でもあります。SEIKOの腕時計製造に始まり、長年にわたり精密加工分野で培ってきた「小・匠・省」の技術を基に、今後も様々な精密部品加工の高精度化と高能率化に貢献していきます。